FACILITY
We take pride in our reputation for excellent customer service, quality products, and innovative solutions.
Design
A highly innovative and experienced design team makes sure the international standards are adhered to throughout the process
Design Capabilities & Facilities
Short Circuit Strength
Transformer windings are severely affected by electromagnetic force due to short-circuit currents passing through the windings.
Short-circuit tests have been conducted on some of our power transformers by KEMA in the Netherlands. This shows the integrity of Design calculations and process followed by Federal Power Transformers.
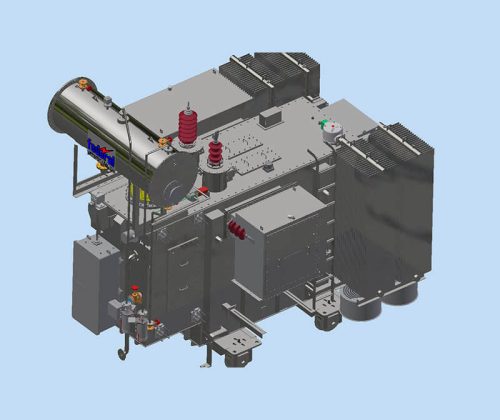
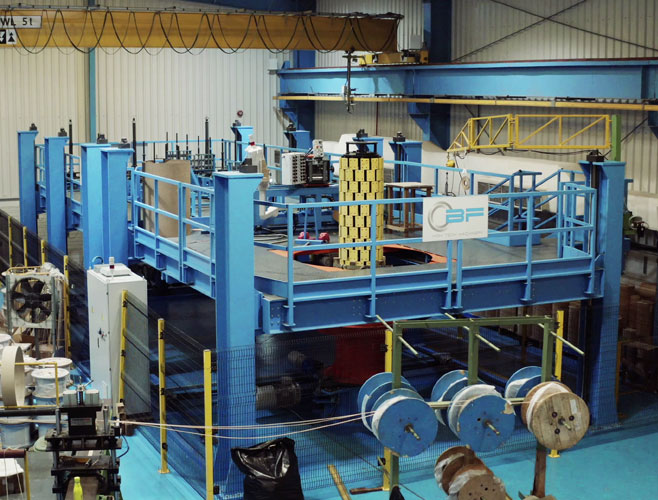
Manufacturing
The core employs a mitred step-lap design ensuring minimum noise and loss level
The Core
Windings & Insulation
All windings are manufactured to exacting standards in order to maintain strict dimensional tolerances. Clamping to a pre-determined load pressure during manufacture ensures that each winding is able to withstand the excessive axial forces which may result from external and short-circuit events.
All principal components of insulation are prefabricated from electrical grade insulating board and are pre-shrunk to ensure electrical and mechanical stability throughout the temperatures found in operational service.
The completed core-coil assembly is dried in a PLC controlled vacuum drying chamber
Tanking
The completed core-coil assembly is dried in a PLC controlled vacuum drying oven. The dried active parts are fitted into the transformer tank and oil is filled under vacuum through a filtration machine.
Final Assembly
When the tanking process is completed all accessories are fitted.
- Bushings (Oil to Oil, Oil to SF6, Oil to Air Condenser, Porcelain, Plug-in type, Monoblock)
- Conservator with hydro compensator (Air bag)
- Maintenance free breathers
- Other customer specific fittings/instruments
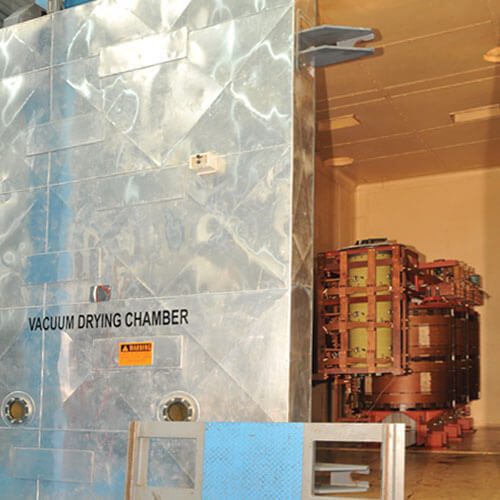
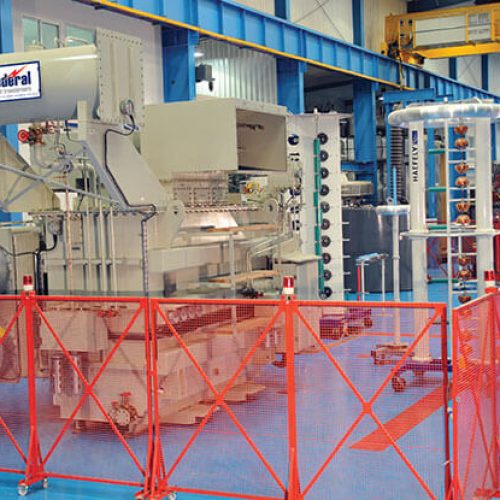
Testing & Inspection
Test laboratory is ISO 17025:2017 accredited and fully equipped with state-of-the-art apparatus to carry out routine, type and special test facilities available.
- Testing at 50Hz and 60HZ
- 2.65 MVA Power Regulator, which when operated in conjunction with the capacitor banks, provides power for temperature rise tests at full ratings for units up to 100MVA 132kV
- 200Hz MG set for induced over voltage test
- Haefely Impulse Test system with Impulse Analysing system type Hias 743
- Haefely Tan Delta and Capacitance Bridge for measuring capacitance and loss angle measurements
- Flash Transformer for SSV Test
- Partial Discharge Test
- Bruel and Kjaer sound level measuring equipment for sound level and spectrum frequency analysis
- SFRA testing
- Oil Testing
Quality Assurance
Quality Management
Federal Power Transformers LLC operates a Quality Management System conforming to ISO 9001:2015 and Transformer Testing Lab accredited to ISO 17025:2017.
Incoming materials are procured from FPT approved sources and subjected to rigorous quality checks as per rigid internal standards based on BS, IEC, FPT standards and practices.
The accuracy and consistency of the product is maintained through strictly following the laid down inspection and test procedures especially in critical areas such as winding, core coil assembly, drying of active parts, tanking and oil filling.
The whole Quality Management System is under constant review and is audited periodically. This is to ensure that at each stage the work is carried out to customer requirements and satisfaction.
EHS Management
Federal Power Transformers LLC has certified OSHAS ISO 45001:2018 by Intertek, a reputed certification agency. Our EH Management System is also approved by Industrial Development Bureau – Department of Economic Development, Abu Dhabi, the local government body.
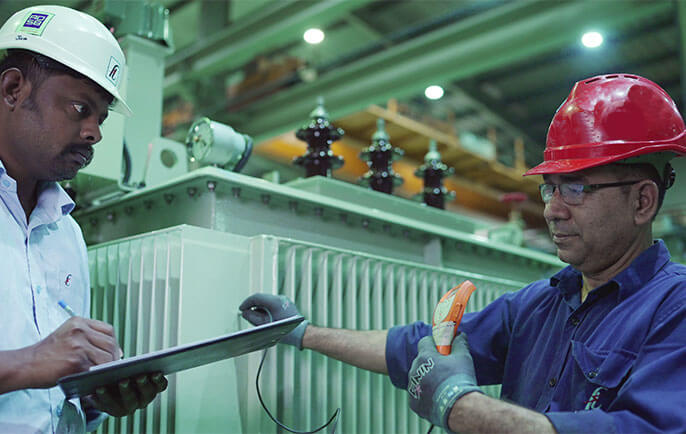